-
-
-
- Services pour bioprocédés
- Services pour centrifugeuse et rotors
- Services pour Mastercycler
- Services pour automates de pipetage
- Services pour congélateurs
- Services pour incubateurs
- Services pour agitateurs
- Services pour appareils de photométrie
- Service de contrôle de la température et de l’agitation
- Service pour pipette
-
-
-
-
- Services pour bioprocédés
- Services pour centrifugeuse et rotors
- Services pour Mastercycler
- Services pour automates de pipetage
- Services pour congélateurs
- Services pour incubateurs
- Services pour agitateurs
- Services pour appareils de photométrie
- Service de contrôle de la température et de l’agitation
- Service pour pipette
-
-
- Centrifugeuses de paillasse
- Centrifugeuses au sol
- Centrifugeuses réfrigérées
- Microcentrifugeuses
- Centrifugeuses multi-fonctions
- Centrifugeuses haute vitesse
- Ultracentrifugeuses
- Concentrateur
- High-Speed and Ultracentrifugation Consumables
- Accessoires
- Tubes
- Plaques
- Gestion des appareils
- Gestion des échantillons et des informations
- Produits IVD
Regarding suitability of Eppendorf bioprocess equipment in GMP-regulated applications, please reach out to your Eppendorf sales representative.
Microbial Fermentation
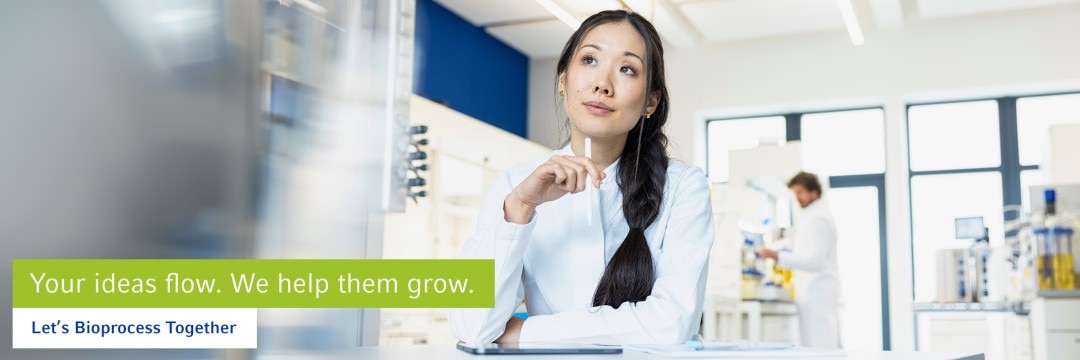
Let's talk bacterial fermentation , let's talk yeast fermentation . Come talk to us, we are all ears.
Lire moins
Eppendorf solutions for microbial fermentation
- Application flexibility: Cultivation of bacteria, yeasts, and other fungi under aerobic, microaerophilic, or anaerobic conditions
- Scalability: Scalable from 60 mL to 2400 L, Eppendorf offers a wide range of bioreactor control systems to help you scale up from the bench to industrial production
- Process optimization: Innovative hardware and software solutions to optimize process control, automate tasks, and harness the power of data
- Time-saving and risk mitigation: BioBLU® f Single-Use Bioreactors for microbial applications can be used as an option with most Eppendorf bioprocess systems to reduce the contamination risk and save setup time
Lire moins
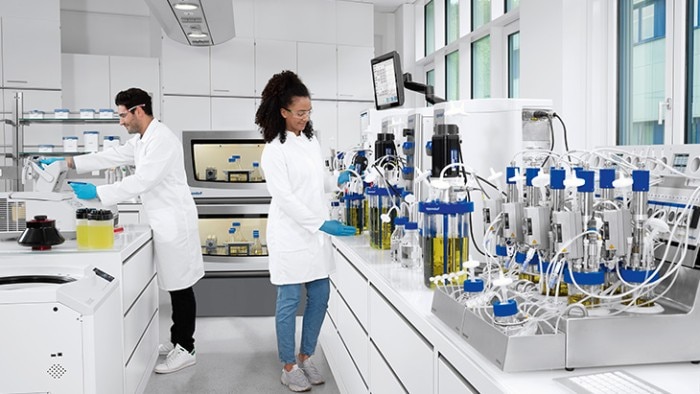
What properties make a bioreactor system suitable for microbial fermentation?
Lire moins
Bioreactors should support high cell densities during aerobic fermentation
Oxygen supply: Essential for an aerobic cultivation to be successful
- Impellers: These are used to agitate and mix a cell culture. The number of blades, speed and diameter can all affect the DO level.
- Sparger: Spargers are tools for gas exchange, specifically for introducing air and oxygen. The type of sparger influences the created bubble size and how effectively oxygen can be transferred to the cell biomass.
- Gassing system: Gasses can be introduced into the bioreactor via the headspace or directly into the culture. This is called overlay and submerged gassing, respectively.
- Baffles: The use of baffles enhances the mixing process. It leads to more turbulent mixing and prevents the culture from vortex mixing by breaking the vortex.
Lire moins
Culture feeding: Needed to encourage growth and microbial production
- Batch: Feeding substrate is only added at the beginning of the fermentation process.
- Fed-batch: Feeding substrate is added at the beginning and in increments throughout the rest of the bioprocess until the maximum working volume is reached.
- Continuous: Substrate is continuously added to the culture, with the continuous harvesting of cells and media to maintain a constant environment.
Fed-batch and continuous culture operation modes offer the possibility to incorporate feed automation and improve your fermentation process. Feed automation can be accomplished by tracking various parameters in real-time to keep track of the culture's metabolic health and automatically alter the substrate concentration with feed pumps. Bioprocess software like DASware® control can be utilized to automate feeding by monitoring important parameters in real-time.
Lire moins
Temperature: Must be monitored and adjusted when necessary
Lire moins
Bioprocess systems should facilitate process optimization
How parallel bioreactor systems can help accelerating process optimization
Lire moins
Lire moins
How single-use bioreactors can help saving development time
Lire moins
How to optimize bioprocess monitoring and control
Lire moins
Bioreactors should support scale-up
How to scale-up your bioprocess
Process development is initially conducted using small volumes until the ideal conditions for microbial production have been found. A scaling up process is then carried out to reach the larger volumes required for production. This procedure is generally carried out in stages, from bench scale to pilot scale through to industrial scale. An important goal when scaling-up is to reproduce process performance across scales.
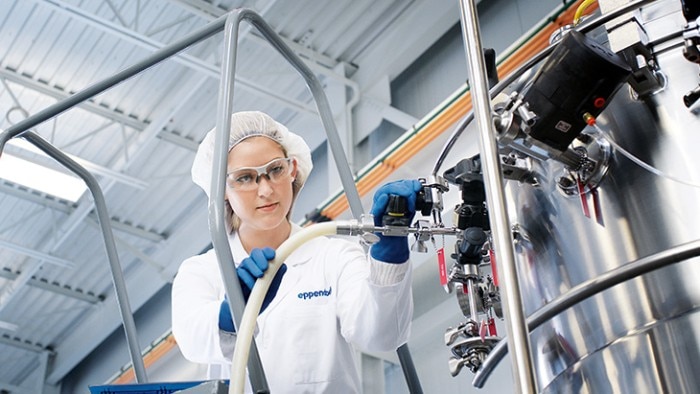
Bioprocess scale-up with the Eppendorf bioreactor systems
Scalable from 60 mL to 2,400 L, Eppendorf offers a wide range of bioreactor control systems to help you scale up from the bench to industrial production:
- Small-scale: The DASbox® Mini Bioreactor System and DASGIP® Parallel Bioreactor Systems cover working volumes of 60 mL to 1.8 L. They facilitate parallel operation of up to 24 bioreactors.
- Bench-scale: The SciVario® twin , BioFlo® 120 , and BioFlo® 320 cover working volumes of 250 mL to 3.8 L.
- Pilot/production-scale: The sterilize-in -place systems BioFlo® 510 , BioFlo® 610 , and BioFlo® Pro cover working volumes of 10.75 L to 2,400L.
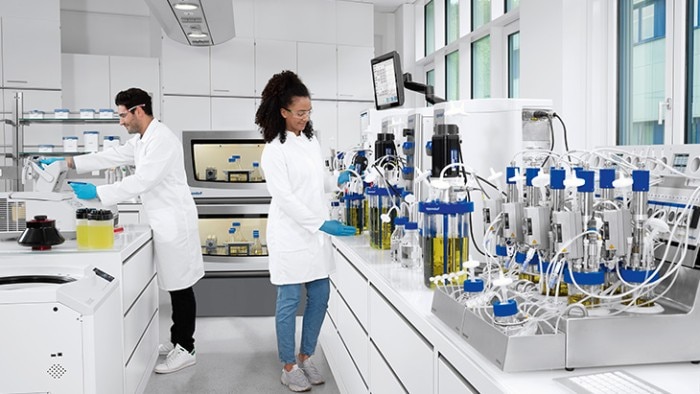
Lire moins
If needed, bioreactors should support microaerobic and anaerobic fermentation
Bioprocessing under anaerobic, microaerobic, and aerobic conditions
- Anaerobic: This describes an oxygen-free environment or a DO concentration of 0 %, and is commonly used in microbial production to manufacture various compounds including ethanol, lactic acid, and acetic acid.
- Micro-aerophilic: Conditions of less than 10 % DO are usually required for micro-aerobes, such as those found in the human gut. Probiotics are frequently produced using this type of fermentation.
- Aerobic: With a typical DO concentration of over 30 %, aerobic fermentation is essential for enhanced growth of many microbial cultures including E. coli.
For some organisms, their cultivation requires mimicking their natural environment. For example, in order to cultivate gut microbiome bacteria and their natural fermentation by-products, bioreactors need to be able to reproduce the microaerobic conditions found in the gastrointestinal tract. This requires fine control of DO levels through real-time monitoring and adjustment.
Lire moins
Find out more
- Webinar: How to tailor your oxygen transfer rate (OTR)
- Application Note: Anaerobic Clostridium beijerinckii fermentation in Eppendorf bioreactor control systems
Lire moins
How our customers use our products
Lire moins